1. Introduction of local resin curing technology.
(1) local field curing and repairing technology is a method for repairing non drainage parts of drainage pipelines. Using glass fiber cloth air bag local molding technology, the glass fiber cloth coated with resin is tightly attached to the mother tube and solidified under normal temperature.
(2) local field curing mainly consists of two kinds of technology, namely artificial glass fiber reinforced plastic interface and glass fiber cloth air bag local molding. Glass fiber cloth gasbag local molding technology is more commonly used, curing resin at damaged point, increasing pipe strength to achieve repair purposes, and providing certain structural strength.
(3) in the trenchless repair of drainage pipelines, it is usually used in conjunction with soil grouting technology.
(4) protect the environment, save resources, do not excavate the road surface, do not produce garbage, do not jam traffic, and make the image of pipeline repair and construction greatly improved. The overall social and economic benefits are good.
Two. Scope of application:
(1) pipes and pipes for reinforced concrete and other materials.
(2) suitable for partial and overall repair of drainage pipelines.
(3) the structural defects of applicable pipelines are presented as rupture, deformation, dislocation, disconnection and leakage, and the interface dislocation should be less than or equal to 5cm. The basic structure of the pipeline is basically stable, the pipeline shape has no obvious change, and the wall body of the pipeline is not solid.
♐(4) suitable for permeable or critical preventive repairs at piping interfaces;
(5) it is not suitable for damage and repair of inspection wells.
(6) it is not suitable for repair of structural defects such as fracture of pipeline foundation, collapse of pipeline, reverse connection of pipeline disconnection, serious dislocation of pipe interface, serious deformation of pipe line and so on.
Three. Construction process:
Detailed steps are introduced:
💛1. Use CCTV to detect single point to be repaired in pipeline.
ꦬ2, allocate a considerable proportion of resin and cut out quantitative glass fiber cloth.
The ratio of resin and excipient 2:1 should be reasonable.
Blanking cloth tailoring: according to the repair pipeline situation, in the waterproof closed room or construction vehicle, the site will cut certain size of glass fiber felt cloth. The tailoring length is about 3.5 times the diameter of the airbag to ensure that the felt cloth overlaps on the airbag. The width of the cut cloth must make it exceed the pipe defect 10cm above and below, so as to ensure that the felt cloth can be clung to the main tube.
3. Lay the glass fiber cloth flat.
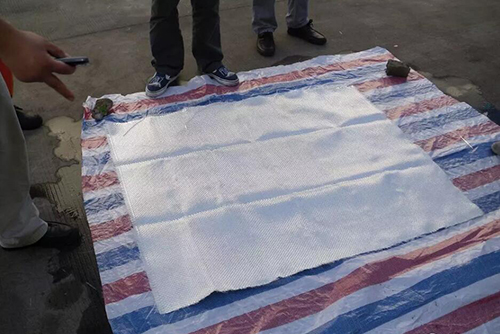
♔4. Evenly spread the resin on the fiberglass cloth.
5. After leveling and folding, the glass fiber cloth coated with resin is tightly bonded on the repaired airbag, and the adhesive tape or the fresh-keeping film is fixed to prevent the falling of the glass fiber cloth;
6." style="box-sizing: border-box">CCTV detection robot The guideline is to pull the air bag to the pipe injury.
𝓀7. Use air pump to inflate the air bag to keep it close to the original pipe.
ꦉ8, wait for a period of time resin curing molding, deflating, pulling out the air bag.
ꦬFour, matters needing attention in the operation process:
(1) 2:1 of resin and excipient should be reasonable.
(2) glass fiber cloth should be prepretreated in vacuum. The volume of the resin should be enough to fill the nominal thickness of the fiber hose and all the space calculated according to the diameter. Taking into account the polymerization of resin and the possibility of infiltration into the gaps and joints of the repaired pipes, the allowance of 5~10% should also be increased.
(3) glass fiber cloth must be fastened on the air bag with wire to prevent slipping of glass fiber cloth when the air bag enters the pipe.
(4) inflation and deflation should be slow and uniform.
(5) during the curing of the resin, the pressure inside the balloon should be kept at 1.5Bar, ensuring that the glass fiber cloth is tightly attached to the tube wall.
(6) resin immersion: use a suitable spatula to evenly mix the resin mixture on the glass mat. The thickness of felt fabric reaches the design value by folding, and the resin is coated on the new surface in these processes. To avoid air entrainment, a roller should be used to press the resin into the felt cloth.
(7) positioning and installation of fiberglass cloth: the resin coated fiberglass cloth is installed through the air bag. In order to form an isolation layer between the air bag and the pipeline during construction, the polyethylene (PE) protective film is used to trap the air bag, and then the glass fiber cloth is bundled on the air bag to prevent it slipping or falling. When the air bag is sent into the repair pipe section, the air pipe should be connected and the inner wall of the glass fiber cloth contact pipe should be prevented. After the balloon is positioned, the air bag is pressurized to expand the air bag, and the glass fiber cloth is tightly attached to the tube wall.The air pressure needs to be kept for a certain time until the felt cloth is completely cured by normal temperature (or heating or illumination).